精密金属部品は、CNC加工をはじめとする様々な精密加工技術を用いて製造されることが多く、一般的にはCNC加工が用いられます。通常、精密部品は寸法と外観の両方において高い基準が求められます。
そのため、アルミニウムや銅などの金属をCNC加工する場合、完成品の表面にツールマークやツールラインが発生することが懸念されます。この記事では、金属製品の加工中にツールマークやツールラインが発生する原因について解説し、潜在的な解決策も提案します。
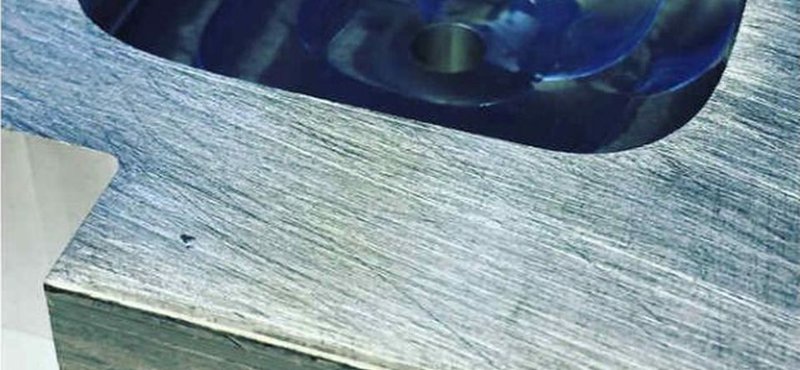
固定具の締め付け力が不十分
原因:一部のキャビティ金属製品では真空固定具を使用する必要がありますが、表面の凹凸により十分な吸引力が得られず、ツールマークや線が残る場合があります。
解決:これを軽減するには、単純な真空吸引から、真空吸引と圧力または横方向の支持を組み合わせたものへの移行を検討してください。あるいは、部品の構造に基づいて代替治具オプションを検討し、特定の問題に合わせたソリューションをカスタマイズしてください。
プロセス関連の要因
原因:特定の製品製造プロセスがこの問題の一因となっている可能性があります。例えば、タブレットPCのリアシェルのような製品は、側面穴のパンチ加工とエッジのCNCフライス加工という一連の機械加工工程を経ています。この一連の工程により、フライス加工が側面穴の位置に達すると、目立つ工具痕が残ることがあります。
解決:この問題のよくある例は、電子製品の筐体にアルミニウム合金が使用される場合に発生します。この問題を解決するには、側面穴あけとフライス加工をCNCフライス加工のみに置き換えることで工程を変更できます。同時に、フライス加工時の工具の噛み合いを一定に保ち、切削ムラを低減します。
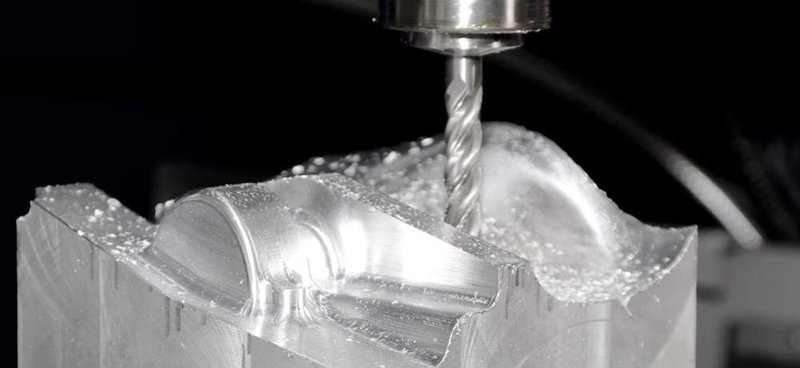
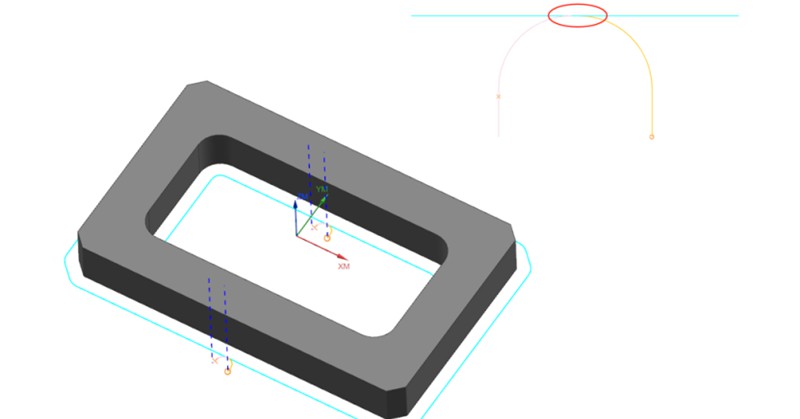
ツールパスエンゲージメントの不適切なプログラミング
原因:この問題は、製品製造における2D輪郭加工段階でよく発生します。CNCプログラムにおけるツールパスの噛み合い設計が不十分なため、工具の入口と出口に痕跡が残ってしまいます。
解決:入口と出口における工具跡を回避するという課題に対処するため、一般的には工具の係合距離にわずかなオーバーラップ(約0.2mm)を設けることが推奨されます。この手法は、機械のリードスクリューの精度における潜在的な不正確さを回避するのに役立ちます。
この方法は工具痕の形成を効果的に防止しますが、製品の材質が軟質金属の場合、繰り返し加工の要素が生じます。その結果、この部分は他の部分と比較して質感や色にばらつきが生じる可能性があります。
平らな機械加工面の魚の鱗模様
原因:製品の平面部に魚の鱗のような模様や円形の模様が現れることがあります。アルミニウムや銅などの軟質金属の加工に使用される切削工具は、一般的に3~4枚刃の合金用フライス盤です。硬度はHRC55~65です。これらのフライス加工は工具の底刃で行われるため、部品表面に独特の魚の鱗のような模様が現れ、全体的な外観に影響を与えることがあります。
解決:平坦度が要求される製品や、凹構造を持つ平面製品によく見られます。解決策としては、合成ダイヤモンド素材の切削工具に切り替えることで、より滑らかな表面仕上げを実現できます。
機器部品の老朽化と摩耗
原因:製品表面に残るツールマークは、装置のスピンドル、ベアリング、リードスクリューの経年劣化と摩耗に起因します。さらに、CNCシステムのバックラッシュパラメータが適切でないと、特に丸みのある角を加工する際に顕著なツールマークが発生します。
解決:これらの問題は機器関連の要因から生じるものであり、対象を絞ったメンテナンスと交換によって解決できます。
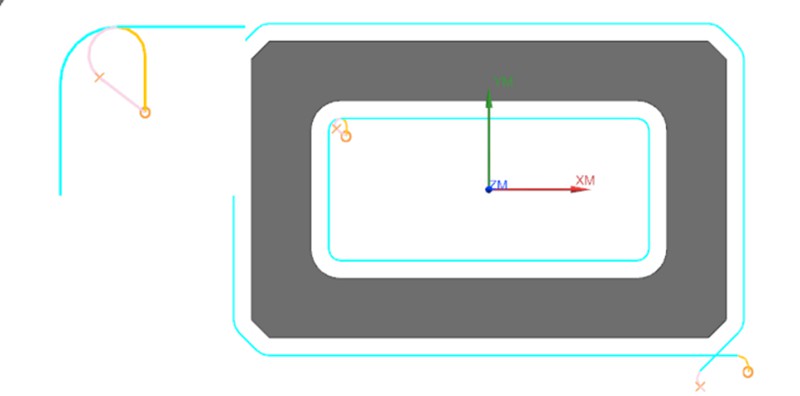
結論
CNC加工による金属加工において理想的な表面仕上げを実現するには、効果的なアプローチが必要です。工具痕やツールラインを回避するには、機器のメンテナンス、治具の改良、工程の調整、プログラミングの改良など、様々な方法があります。これらの要因を理解し、改善することで、メーカーは精密部品が寸法基準を満たすだけでなく、求められる美観も備えていることを保証できます。