製造業は最もダイナミックな産業の一つです。今日、全体的な精度と正確性の向上に向けた絶え間ない努力が続けられており、まさにそれを実現するワイヤー放電加工のようなプロセスは、まさに業界に変革をもたらすものです。
では、ワイヤー放電加工とは一体何なのでしょうか?そして、なぜ製造業にとって画期的な技術とみなされているのでしょうか?以下では、様々な業界で応用されているこの高度な製造技術の基礎について解説します。
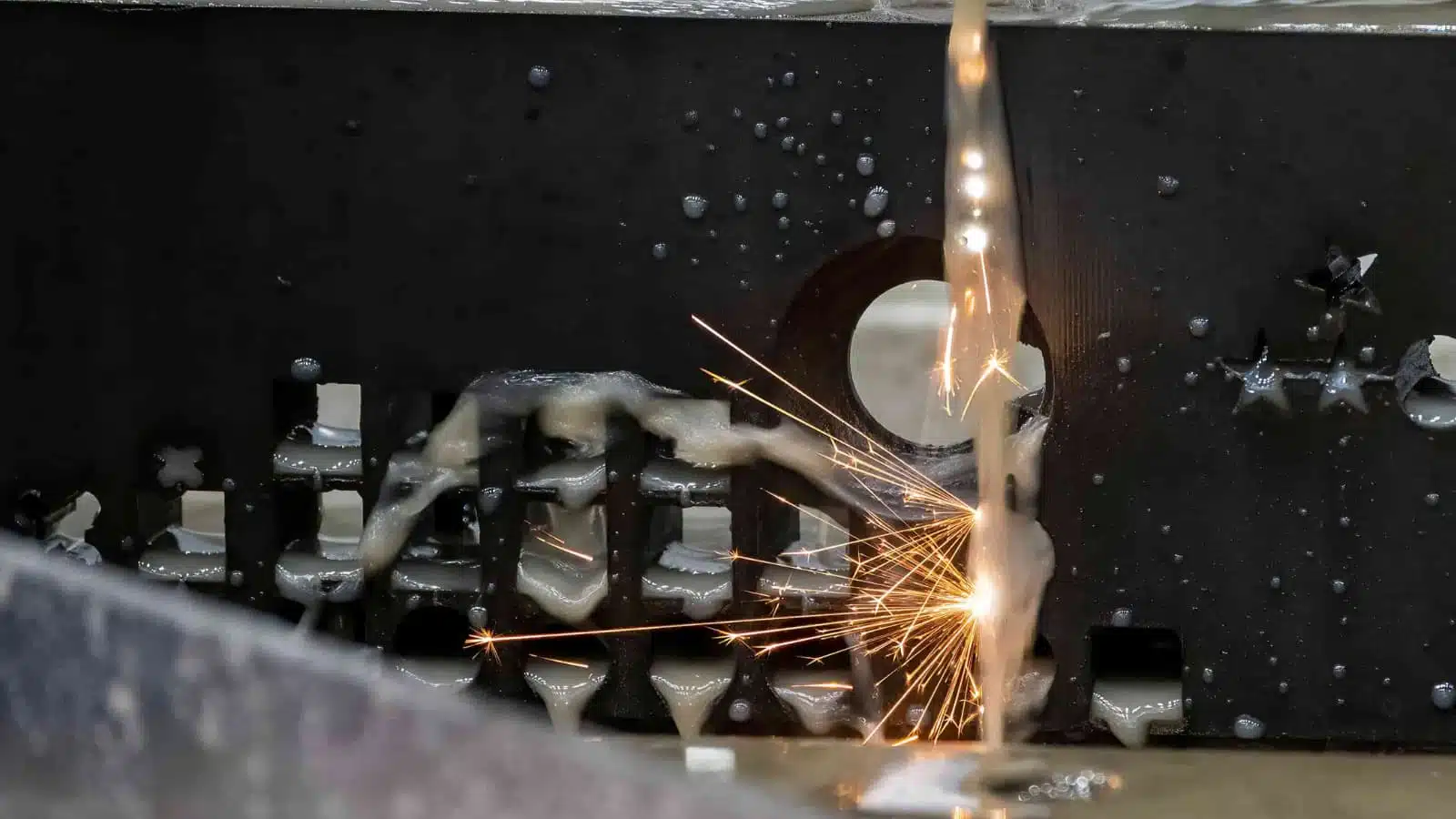
ワイヤー放電加工の簡単な紹介
ワイヤ放電加工(EDM)は、1940年代にソ連の2人の科学者によって開発され、初めて放電加工によって金属を削り取ることに成功しました。この技術は1960年代と1980年代に飛躍的な進歩を遂げ、製造業において商業的に広く普及しました。1990年代後半には、IT技術とCNC技術の進歩により、ワイヤ放電加工機のコンピュータ化が進み、効率と精度が向上しました。
今日、ワイヤー EDM は、従来の加工方法では実現できない精巧なデザインや複雑な形状を実現できることで知られ、航空宇宙、自動車、医療などの業界では欠かせないものとなっています。
ワイヤー放電加工プロセス
ワイヤ放電加工(EDM)は、制御された電気火花を用いてワークピースの微細な部分を溶かす精密な加工方法です。ワイヤ電極(通常は真鍮または亜鉛メッキ材)が火花を発生させ、所定の経路に沿って移動します。その利点は、物理的な接触なしに加工できるため、ワークピースと工具の両方に損傷や跡が残らないことです。
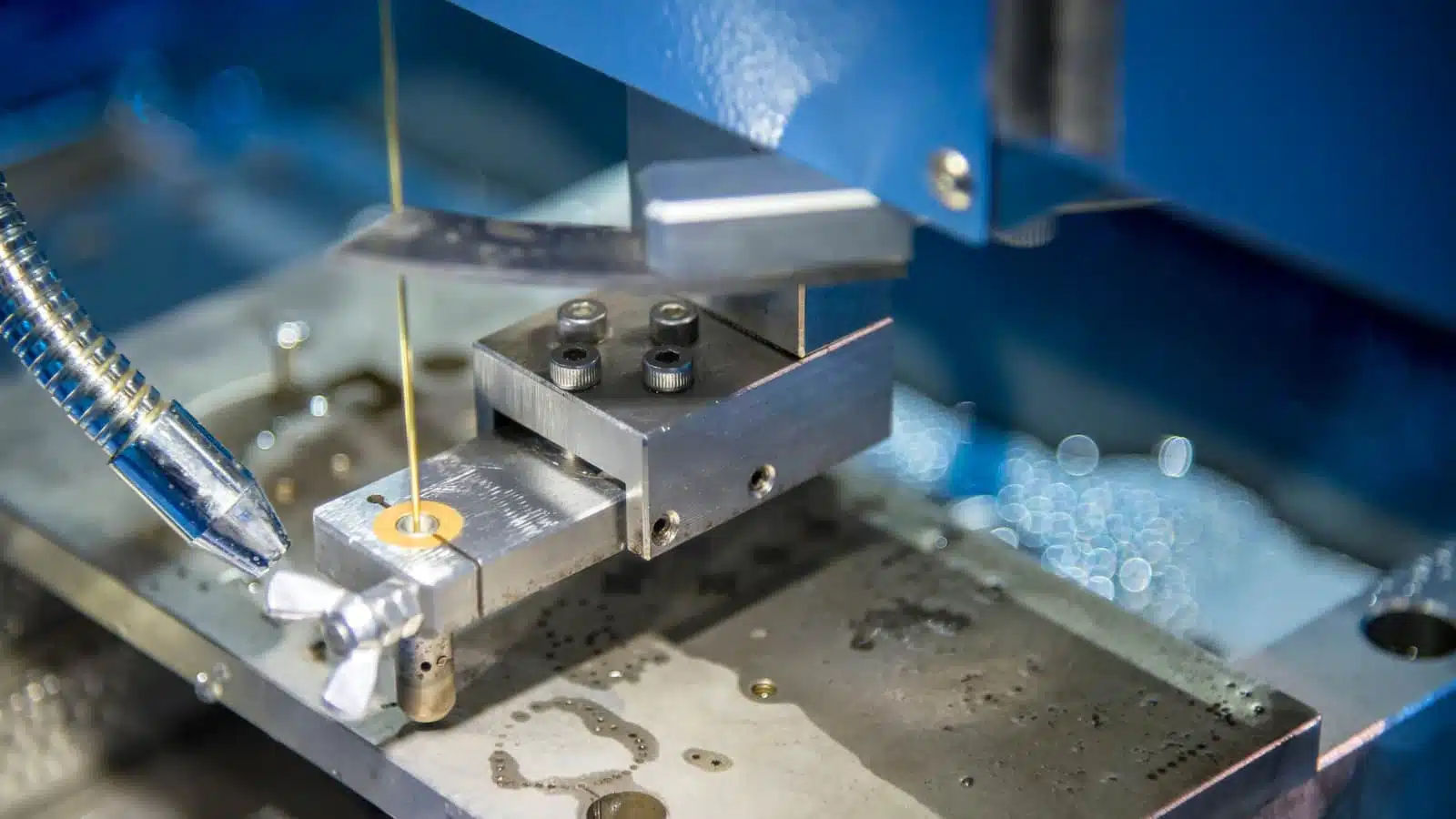
EDMの仕組み
EDMは放電加工の熱エネルギーに依存しています。この放電加工によって加工対象物は融点まで加熱され、微細なプラズマチャネルが形成されます。これらのチャネルはマイクロメートルサイズであることが多く、すぐに消滅してしまいます。
EDMプロセスは、通常は脱イオン水などの誘電体媒体中で行われます。この流体はワークピースを冷却し、蒸発した材料を除去することで、連続加工を可能にします。
ワイヤー電極の重要性
ワイヤー電極は、カッターと導体の両方の役割を果たすため、非常に重要な役割を担っています。真鍮や亜鉛などの素材でコーティングされているため、高温での反応にも耐えます。コンピューター制御により、歪みを最小限に抑え、高精度で正確な切断を実現します。
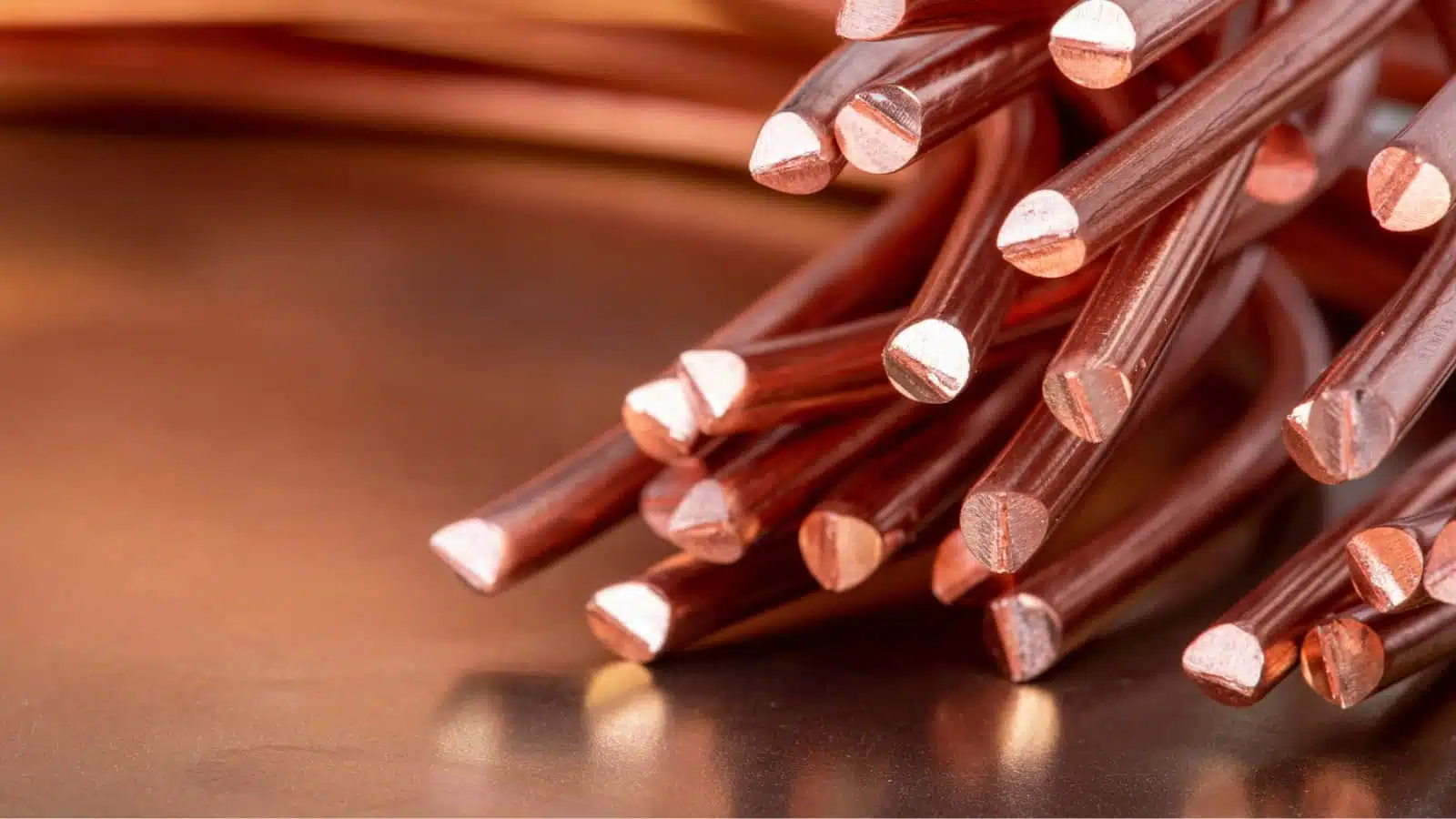
ワイヤー放電加工の許容範囲
ワイヤーカットは、最も精密な製造工程の一つです。そのため、厳しい公差が求められることは珍しくありません。実際の公差は、プロジェクトの複雑さ、加工能力、オペレーターのスキルなど、いくつかの要因によって異なります。
ただし、標準および許容誤差は、多くのメーカーが従う業界のベンチマークです。
標準公差と微細公差
標準許容差
線形許容差: 通常、±0.005 ~ ±0.001 インチ (0.127 ~ 0.0254 mm) の範囲で、穴、スロット、プロファイルなどのフィーチャの許容偏差を示します。
穴径許容差: 通常、±0.0005 ~ ±0.001 インチ (0.0127 ~ 0.0254 mm) の範囲で、機械加工された穴が規定の直径内に収まるようにします。
細かい許容範囲
線形許容差: 通常 ±0.0002 ~ ±0.0001 インチ (0.0051 ~ 0.00254 mm) の範囲のミクロン レベルの精度を実現します。これは最高の精度が求められるアプリケーションにとって重要です。
穴径許容差: ±0.0001 ~ ±0.00005 インチ (0.00254 ~ 0.00127 mm) の範囲で、Wire EDM の優れた精度が際立ちます。
ワイヤー放電加工における許容誤差に影響を与える要因
ワイヤーEDMはミクロンレベルの精度で知られており、複雑な用途に最適です。しかし、その精度は一定ではなく、いくつかの要因に左右されます。
•機械の安定性: 安定した機械は切断動作の精度を高めます。
•線材の品質と直径:純度、直径、電気特性は加工プロセスに影響を与えます。最適な結果を得るには、線材の品質と直径のバランスが重要です。
•ワークピースの材質: 一部の材質は機械にとってアクセスしやすいですが、材質の選択はアプリケーションのニーズに合わせて行う必要があります。
•フラッシュ条件: 誘電体媒体の流れは、加工プロセスの品質に影響を与え、材料の除去、一貫した放電、および効果的な熱放散に役立ちます。
•機械の校正とメンテナンス:機械の性能は極めて重要です。優れた機械と熟練したオペレーターは、最高の公差を達成する上で不可欠です。
•熱安定性:ワイヤ放電加工の精度を維持するには、制御された電気アークが不可欠です。熱的不安定性は精度を損なう可能性があるため、安定した加工条件を維持することが非常に重要です。
ワイヤーカットに最適な材料
鉄金属
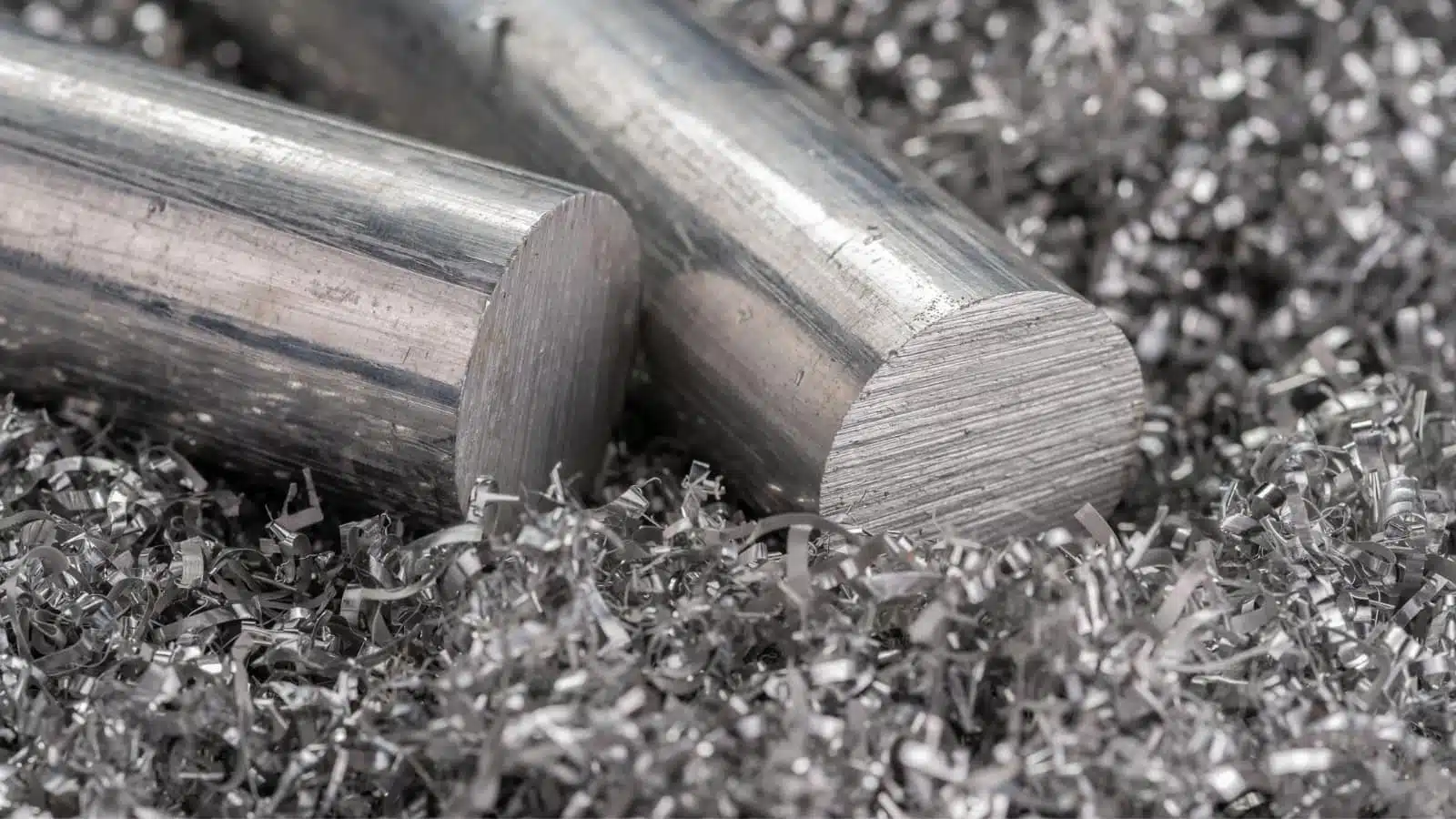
ステンレス鋼
優れた耐久性と優れた導電性を兼ね備え、耐腐食性にも優れているため、様々な産業で求められている素材です。機械加工においては、精密で精緻な設計との相性が際立っています。
工具鋼
工具鋼は、その優れた硬度特性で知られ、多くの重工具や精密部品の基盤となっています。その固有の強靭性と電気特性が相まって、複雑なディテール加工や長寿命の切れ味を実現するのに最適です。
炭素鋼
金属分野において多用途に用いられる炭素鋼は、他の鋼材に比べて加工性は劣るものの、適切な電極の選択と操作パラメータの設定により、完璧な仕上がりを実現できます。その手頃な価格と優れた性能により、多くの産業で欠かせない存在となっています。
合金鋼
合金鋼は様々な元素の融合体であり、その性能は構成成分の織りなすタペストリーのようなものです。独自の配合によって、強度、耐久性、そして加工性が向上し、多様な用途に最適な選択肢となります。
非鉄金属
チタン
しばしば「宇宙時代の金属」と呼ばれるチタンは、その堅牢性と高い融点により、従来の機械加工では加工が困難です。しかし、精密工具で加工することで、精巧でありながらも優れた強度を持つデザインが実現し、航空宇宙産業や医療産業で好まれています。
アルミニウム
軽量金属の寵児であるアルミニウムは、優れた導電性と展性で高く評価されています。加工が容易なだけでなく、重量による負担なく強度を確保できるため、輸送から包装まで、あらゆる産業で重要な役割を果たしています。
銅
銅は、卓越した導体として、多くの電気・電子工学の驚異の中核を成しています。その自然な赤みがかったオレンジ色の色合いと、精巧な部品に成形できる性質により、電子機器から装飾芸術まで、あらゆる分野に欠かせない存在となっています。
真鍮と青銅
黄金色に輝くこれらの合金は、見た目の美しさだけではありません。優れた電気特性により、装飾的な宝飾品や精巧に作られた電子部品など、精密さと美しさが融合する部品の素材として最適です。
現代のエンジニアリングにおけるワイヤー放電加工の主な用途
ワイヤー放電加工は、多様な材料に対応できる汎用性と、精密なディテールと厳しい公差を実現できる能力から、注目を集めており、現代の製造業において極めて重要な役割を果たしています。主な用途は以下の3つです。
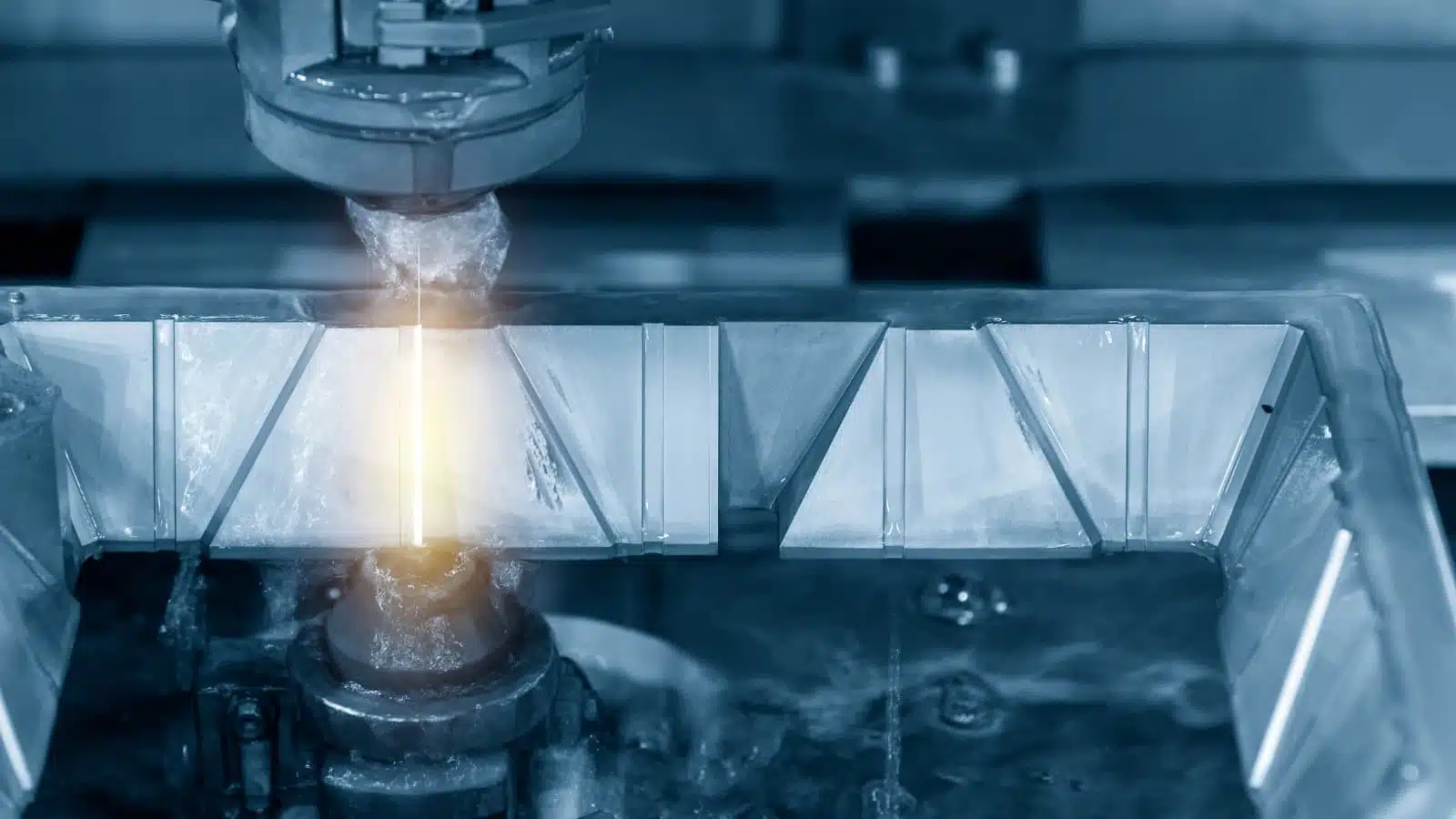
精密部品製造
厳しい公差が求められる高精度部品の製造に広く採用されています。複雑な形状、微細なディテール、そして様々な材料を用いた微細な特徴の加工に優れています。
航空宇宙、医療、自動車、電子機器などの業界では、ギア、ノズル、コネクタ、複雑な金型などの重要なコンポーネントを作成するためにワイヤー EDM を利用しています。
工具・金型製造
ワイヤー放電加工(EDM)は、射出成形からスタンピングまで、金型、ダイ、特殊工具の鍛造に重要な役割を果たします。正確な寸法を維持し、鋭角を彫刻する優れた能力により、大規模生産において最高品質と均一性を保証します。
プロトタイプ開発
迅速かつ正確な試作を実現するために、エンジニアやイノベーターはワイヤー放電加工(EDM)に注目しています。これにより、設計検証と厳格なテスト段階が迅速化されます。
ワイヤー EDM で彫刻されたプロトタイプは最終製品を厳密に反映しており、製品進化サイクルにおけるその重要性が強化されます。
これらの中核分野における強みにより、Wire EDM の正確で精密な機能は、数多くの業界で幅広く活用されています。
•医療機器製造
•電子機器およびマイクロコンポーネント
•航空宇宙および航空
•宝飾品と時計製造
•自動車産業
•エネルギー部門
•金型修理
投稿日時: 2023年12月12日